Revamping of the continuous casting machine No. 1 at PJSC «Severstal»
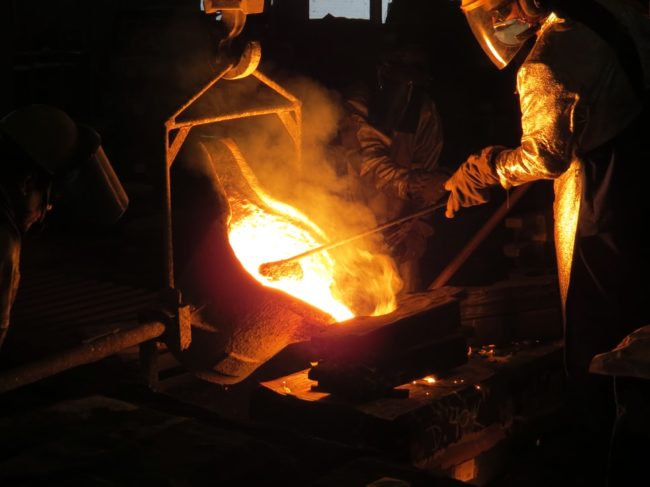
From October 26 to November 12, 2020 in association with our partners – the machine-building enterprise «ASM Group Ltd» (Cherepovets), the Reconstruction of the continuous casting machine No. 1 was carried out as part of revamping of the continuous casting plant at PJSC «SEVERSTAL».
The reconstruction is the next stage of the continuous casting machine long-term modernization program at PJSC «SEVERSTAL».
The concept of the modernization program is to carry out a series of reconstruction measures aimed at setting sustainable development in short time with minimum costs, including Suspensions of Production, and eventually leading to a significant technical condition renewal of all the continuous casting machines in the plant.
The previous program stages included: upper part of the roller guide continuous casting machine modernization, crystallizers and mold oscillating unit replacement, equipment reconstruction of the torch cutting machines, continuous casting machine shift to a closed-loop equipment cooling system.
Current reconstruction phase included a radical modernization of the radial section of the continuous casting machine roller guide with the roller sections replacement with medium supports. A modern secondary cooling ingot system has also been implemented, which includes a multi-loop manifold installation and ingot cooling control using a mathematical model.
The following set of technical measures was implemented:
- Roller sections No. 3-6 replacement (radial section of the Continuous casting machine) with new ones three point rollers.
- New cooling circuits for the middle roller supports were arranged and the temperature of the coolant was monitored. New IFM flow and temperature sensors have been introduced to the cooling control of the roller supports in sections 3 to 6. The data from the flow sensors is collected and displayed to the operator via the new ET200 remote I/O station.
- In order to meet the quality requirements of continuous casting, the secondary cooling zone has been reconfigured into a multi-row zone with automatic width adjustment of the secondary cooling zone during casting. New block-type water-air nozzle devices were installed in sections 3-9.
The WinCC Open Architecture software from Siemens was used as a platform for the operation and integration of the mathematical model. The control system calculates and monitors the cooling process of the continuous casting, the control actions in dynamic and static modes do not lead to overcooling or overheating of the ingot. Moreover, a special server and IBA workstation have been installed to archive its operation parameters. The CPU modules of existing controllers were upgraded and additional ET stations were added to accommodate the increased number of signals. The new equipment was integrated into the continuous casting machine automated control system.
We would like to express sincere gratitude to the Executive Director of the ASM GROUP, V. N. Popovich, for the high professionalism and invaluable contribution to the implementation as well as KONSOM GROUP members: Avdonin, V. Y., Streletsky, G. Y., Bochin, V V., Khomlev, S.V., the commissioning department and everyone who helped with the project realisation. Well co-ordinated work allows to overcome successfully all the difficulties and to accomplish the mission in time.